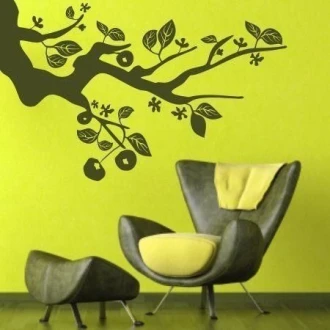
Lean Management - we admit that the term sounds puzzling, but the principles of management work perfectly well in most companies and companies, both large and small! In our today's article we will answer the question - what lean management actually is and discuss the basic tools useful in applying this method.
Lean management is a concept that has been developed over many years and is the result of many improvements and improvements. Its origins date back to the 1940s, when the Toyota Production System was created, based on the principle of creating products of the highest quality while minimizing waste of energy, materials and processes.
In short, the term "lean management" is a philosophy, a set of principles to eliminate the waste of any work that does not bring direct value to production quality. Currently, the lean management method is widespread in many different industries. It is an extremely universal method, so you can apply it in any business or production process, from production to marketing and software development.
That is why we have prepared an article which clearly explains what the two most popular Lean Management methods are - 5S, Kaizen and Kanban.
Check them and apply them to your company or company!
5S is a visual management method, which is based on an orderly workstation organization. It has been proven that good organization and order have a fundamental impact on the productivity of employees, therefore the 5S method is worth applying both in production halls and office spaces.
The aim of 5S is to establish and maintain order and discipline in the workplace. 5S is one of the most important elements of good management. These are basic actions for the benefit:
The 5S method involves five steps that will help us implement a perfect organization in our workplace, whether it is a production hall or an office station. The first three "S" determine how to put our workplace in order. They define the system we will use. The last two "S" indicate how to maintain and improve the system.
The first step in implementing the 5S method is to identify and assign all the objects at the workplace. It also assumes minimizing unnecessary elements by removing them. These may be unnecessary elements of the machine park or office accessories.
The main goal of this step is to reduce the unnecessary movement and physical effort of employees, which would be spent on searching for necessary objects and documents. This will be facilitated by visual control, which involves the use of border lines, plates, shadow boards and coloured magnets to determine a fixed location for each object or machine.
Keeping workstations clean. This step can be combined with an inspection and audit to detect possible irregularities and quickly eliminate them.
Defines standards of observance of the first three steps of the 5S method by creating visual instructions, thanks to which the employee's change of job and its implementation to work will proceed quickly and without unnecessary disruptions.
Maintaining the improvements at the workstations. All employees participate in this step, and the continuous improvement process includes the possibility to make changes and improvements to make them even more effective and efficient!
To introduce the 5S method, accessories such as special marking tapes, shadow boards and dry erase boards 5s adapted especially for this method will be useful. Thanks to them, it is easy to introduce 5S methods in your company or office!
Kanban (jap. sheet of paper) is a method of production control that involves organizing the production process in such a way that each department produces exactly as much as is needed at the moment. Applied skillfully, it increases productivity and shortens the time of order delivery to the customer.
Kanban is a method based on visual management - a kanban board with a layout divided into activities, e.g. "to do", "in progress" and "ready", will be useful for its introduction. With its help we can show both a simple process and the work of one team, but also this complicated, requiring the involvement of many teams and specialists.
The introduction of the Kanban method allows effective production optimization. Most often this method is described by the password "7 times none". Its aim is to lead to a situation where there will be no shortages, inventory, delays, queues, inactivity, unnecessary activities and control and unnecessary movements in the organization.
To introduce the Kanban method, accessories such as special marking tapes, shadow boards and dry erase Kanban boards adapted especially for this method will be useful.
The principle of kaizen is to improve and change for the better the ongoing work. The aim of the changes is:
Achieving these objectives leads to more efficient work and can improve ergonomics and safety at work. Minor actions to improve our processes are the basis of Lean Management. The company should cyclically improve its functioning, and the best way to do this is to continuously work in this direction. However, for this to be most effective, each of the company's employees must be focused on improvement and constantly look for its possibilities.
When introducing the kaizen method to the company, tables with SWOT analysis or competence matrix will certainly prove useful.
product manager at Wallyboards
Kinga is the heart of our team – she’s the one you’ll most often speak to when you write or call Wallyboards. With passion, she helps customers choose the perfect products for their home or office, sharing her knowledge about features and practical uses. Her experience and dedication mean even the most technical questions get quick and accurate answers.